How Does ERP Improve A Company’s Business Prospects and Profitability?
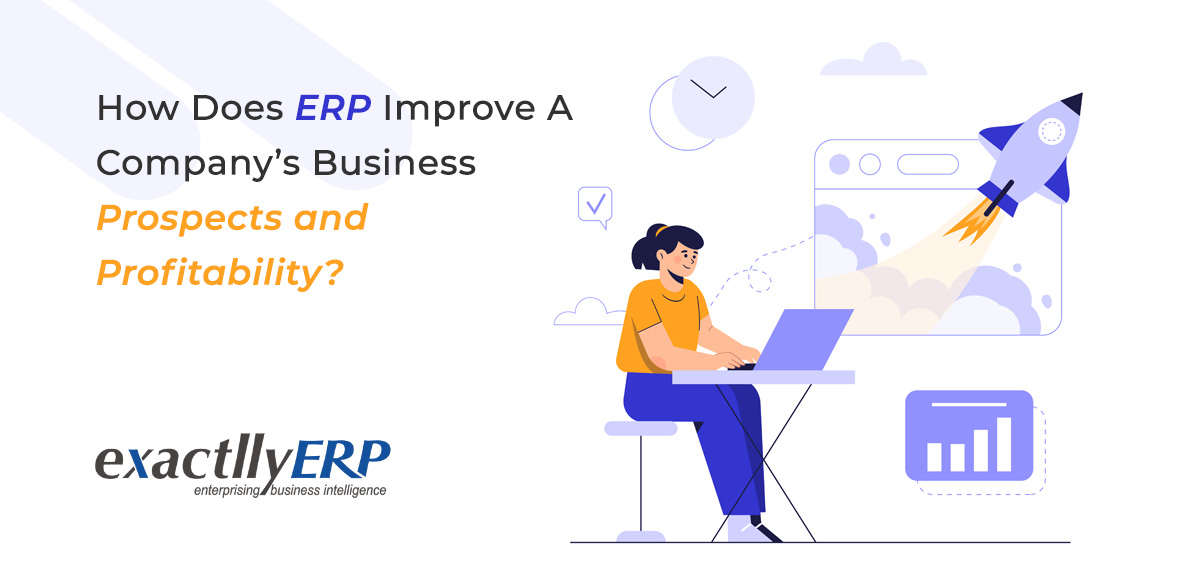
Business and Profitability
While many big corporations have already implemented ERP solutions, small and mid-size organizations are still mulling over the implementation of a full-fledged ERP system. The major deterrent is the risk of business and profitability failure due to poor processes and the inability of the management and employees to adopt the new system.
ERP systems facilitate resource allocation and plan production schedules. They have a huge potential in improving the business and profitability prospects of a company by making its processes efficient. Many manufacturing and distribution companies employ ERPs for increasing productivity and improve decision-making. Let us discuss the various challenges faced by businesses today and find out how ERP provides an answer to all their problems.
Challenges faced by Businesses today:
-
Raw Material –
With increasing production capacity, the demand for raw materials obviously increases. But when there are multiple raw materials, micromanaging every type of raw material becomes a daunting task. Such business and profitability processes are often met by supply hiccups thus disrupting the production cycle. In addition to that, the raw material market is becoming highly volatile with constant price fluctuations. To save cost, the manufacturer must pick up the right amount of quantity from the market. Quality of raw material and the in-process item is another significant matter concerning production managers which affects the final product quality.
-
Revenue Growth –
Increasing competition and the demand for the high-quality product has been keeping a check on revenue growth of companies. Changing technology and process improvement demands continuous investment from businesses which is making it difficult for business and profitability owners to increase their top line. Moreover, suppliers are growing at a faster rate than the market resulting in a shrinking market share.
-
Maintaining Profitability –
Increasing raw material costs is making it difficult to maintain profit margins. High-quality processes demand the purchase of new machinery, training of employees, and hiring skilled labor. Moreover, small-scale businesses do not have the advantage of economies of scale in contrast to large-scale manufacturers. All these issues are responsible for diminishing profit margins.
-
Research and Development
R&D initiatives play an important role in achieving breakthroughs in technology and product. Small scale businesses cannot afford to invest time or money in R&D activities as it starts affecting the cost of their end-product. Their best effort is focused on curbing the cost of existing processes and increase the customer base to stay competitive.
-
Changing Customer Demand –
Customers today have a lot of choices to procure the product. They want a high-quality product at competitive prices on short notice. A small-scale businessman is the first one to face the crunch in times of economic crisis as customers have better control over the market. Manufacturers need to anticipate customer demand and be the first ones to bring the product to market.
What does an ERP do?
-
Reduce Cost and Streamline Processes –
ERP system helps you to cut down wasteful processes. We often see information being generated from different departments of a company. Merging them becomes a humongous task without a common integrated system. Besides eliminating redundant processes, ERPs devise a smoother way of conducting a process. It weeds out inefficiency in the system and introduces a faster way of accomplishing a task.
-
Faster Response to Disruptions –
ERP is an integrated system that helps executives to respond quickly to disruptions. Disruption can be caused by any technical glitch in manufacturing, production flaw, raw-material shortage, and machinery breakdown. ERPs are enabled to detect these gaps so that managers can quickly come up with a solution. It also stimulates them to mull over redesigning the supply chain so that key customers don’t have to face the consequences of disruption.
-
Production Planning and Inventory Management –
ERP system is designed to do production planning, execution, quality check, and maintenance. It helps you to identify business and profitability processes that form a relation between production and inventory management. It allows you to acquire the right quantity of raw materials, schedule the purchase of equipment, and meeting human resource requirements. Furthermore, it enables you to produce an appropriate quantity of products.
-
Eliminate Manual Data Entry –
Manual data entry is time-consuming and is a major source of diminishing productivity of small-scale organizations. As the business and profitability grow, data entry demands increase. Manual data entry is prone to frequent data errors. ERP systems have centralized data management that immediately removes duplicate data entry thus helping your organization to increase efficiency and cut down man-hours.
-
Customer Service Levels –
Maintaining customer service level is the priority for any successful business. Customer service is directly related to your inventory management and work in progress processes. When ERPs detect a significant error in production, the chances of passing flawed products to customers decrease with limited inventory. Similarly, fewer items will get defected if processes are in control. This ultimately saves rework labor thereby increasing the cost of the product. Therefore, ERP will help to curb your operating expenses, meet customer service levels and delivery dates.
-
Resource Utilization –
Every business has limited resources to meet customer demands. Resources include your machinery, inventory, human capital, processes, and technology. If these resources are not utilized to their full potential, it affects your quality and increases the cost of production. A business serving multiple customers often switches its production modes. It means you have to constantly realign your equipment configuration besides reducing downtime. ERPs help you to follow the best possible solution depending upon the customer that may include producing it yourself, subcontracting, or purchasing it.
-
Better Reporting and Regulatory Compliance –
An ERP system manages information from different departments through a centralized database. It offers managers better visibility helping them to generate improved reports. More rapidly growing ERP systems are cloud-based ERP system that allows real-time, synchronized and automated reporting. There are various parameters involved in a production that must meet government regulations, laws of the land and ensure transparency. ERP solutions allow the managers to be in a better position to manage risk and regulatory standards.
The end goal of ERP:
The end goal of the ERP system is to integrate and collaborate seamlessly with different departments to deliver a suitable and affordable product. Businesses should run with the aim of profitability rather than sustainability. ERP systems manage a huge volume of company information to gain business insights and make well-informed decisions.
ERP does not change but improves the way you work. One can say, it helps to design efficient business processes and use ERP to build upon them. ERP combines with existing high-quality business processes and fine-tunes them. Though workers are resistant to change, one can certainly educate and train them to use the new technology.
However, you have to be realistic while implementing an ERP solution. There is no system that can bring a sudden change in your business processes. You must have a strategic plan in place before implementation or before you even start looking for a vendor. exactllyERP is one of the top providers of ERP, to know more about Exactlly, Contact Us and get Free Demo.